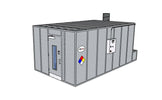
Best Practices for a Safe Processing Lab
, by BVV Team, 6 min reading time
, by BVV Team, 6 min reading time
To protect workers, lab personnel, and customers alike, it has been left up to employers and decision-makers to compose their safety protocol to align with the general requirements of any product processing plant - with added measures to address the unique obstacles of this industry. Here are 3 general topics to help promote Good Lab Practice (GLP)
The extraction and processing industry has come a long way from where it was only a couple of years ago. With the increase of legalization, both medically and recreationally, there is a greater need for regulation in the processing workplace.
Most states that have legalized the industry have yet to implement any form of structured protocol and standards for the operation of a safe processing lab. To protect workers, lab personnel, and customers alike, it has been left up to employers and decision-makers to compose their safety protocol to align with the general requirements of any product processing plant - with added measures to address the unique obstacles of this industry.
Here are 3 general topics to help promote Good Lab Practice (GLP):
Have you trained your employees? Have you identified the potential hazards they may come across on a day-to-day basis? Smaller operations may deem safety measures and training unnecessary, but one small mistake can lead to an employee being seriously hurt. A lab can be a dangerous environment due to the volatility of the solvents used to strip the plant of its valued material and other down-the-line processing. Oftentimes mistakes can be managed and avoided with the proper training.
Whether you perform alcohol, hydrocarbon, or CO2 extraction, it is important to review your company’s SDS (Safety Data Sheet) with all your employees. The hazards will vary from lab to lab and it is vital to identify hazards specific to your processes, such as the extreme extraction conditions of supercritical CO2, the high vapor pressure of hydrocarbons, the neurotoxicity of alkanes, etc. In addition, make sure your employees are well prepared in case an incident does occur. Do they know whether a problem is safe to solve immediately or if it is unstable and requires the attention of an official safety department? You can set your employees up for success by educating them on the differences between manageable failures and critical failures that require focused attention by the right department. For manageable failures, ensure your employees are well equipped with not only the proper PPE but with the tools to implement quick fixes e.g., wrenches, screwdrivers, extra clamps/nuts/bolts.Common problems, like a column gasket leaking, may occur and often can be fixed with simple solutions (in the instance of a gasket leak: the simple tightening of a clamp.) Ensuring your operators are well prepared is key to a safe work environment.
Processing equipment will require some maintenance ever so often. Ensuring routine maintenance can prevent a large system failure that cannot only cost you weeks of production downtime but also prevent injury. Here are some examples of equipment to be mindful of:
There are dozens of variables that come to mind when discussing product handling, but we will name a few.
Growers spend months tending to and caring for their plants – it would break their soul for a lab to toss their precious material into a sweaty, impermeable plastic bag. Biomass should be stored in an environmentally controlled room in proper storage containers. Proper storage can help mitigate microbe growth, prevent pest infestation, and most importantly preserve the precious trichomes. Improper handling will not only leave you with a lesser potency but can also result in the addition of harmful mycotoxins and foreign invaders that will deem your product unsafe for sale once reviewed by an analytical lab.
Another common malpractice would be the improper removal of solvents from an extract. The final step of a BHO/PHO extraction is the recovery process. This is where the solvent saturated extract is exposed to low heat and deep vacuum. These two variables ensure most of the solvent is recovered from the extract solution. Some operators would prefer a runnier, solvent saturated product, but ultimately the solvent must be recovered. Never walk around a lab with an off-gassing Pyrex dish. The solvent-rich extract must remain in the extraction space until the solvent poses no threat of combustion.
Even after recovering the solvent, the product must undergo another process called purging. This process of purging is essential for staying compliant with the allowable PPM of residual solvent. Often extracts are placed in a vacuum oven where the remaining PPM of solvent is removed via gentle heat, deep vacuum, and agitation/flipping of the extract. Never purge an extract on a hot plate or oven, more so in any oxygen-rich environment. Doing so may have deadly consequences and is the most common mistake made by amateur extractors.
Ultimately, safety procedures, handling knowledge and precautionary measures are in place to protect you, your employees, and your end consumers. With this article, we have barely scratched the surface of this overarching and important topic, so we invite you to reach out to us for any more information and guidance. Call us at (331) 239-2285 or e-mail us at support@shopbvv.com.
Recommended lab safety training courses:
Lab Safety | OSHA Certificate Course (oshaeducationcenter.com)
Hazardous Chemical Information | OSHA Certificate Course (oshaeducationcenter.com)
Process Safety Management | OSHA Certificate Course (oshaeducationcenter.com)
Egress and Emergency Action Plans | OSHA Certificate Course (oshaeducationcenter.com)